Grease Extraction Duct Clean (GEDC)
When Was Your Grease Extraction Last Cleaned?
Cleaning your kitchen extraction system is a legal requirement.
Grease extraction duct cleans are normally undertaken out of service hours. When undertaking a full extraction system clean, both the interior and exterior of the canopy hood are degreased thoroughly with particular attention given to the baffles where heavy grease build up usually materialises. The baffles are removed, inspected and soaked in a powerful cleaning solution and replaced when they meet our safety standards. All areas of the system are cleaned.
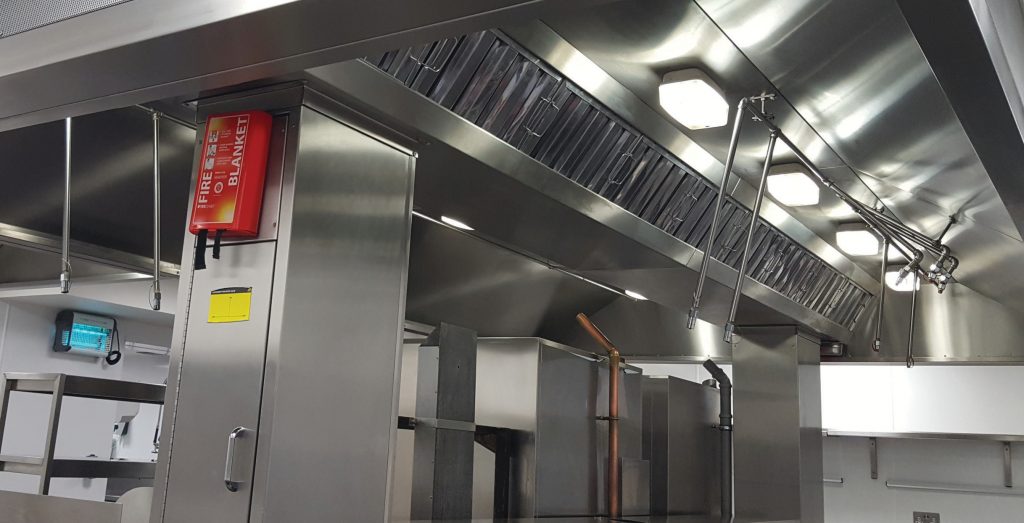
Benefits of an Insuraclean kitchen grease extraction duct clean:
- Assists compliance with fire safety legislation
- Assists compliance with buildings insurance policies
- Significantly reduces the potential risk of fire within the system
- Reduces operating costs by prolonging working life and increasing efficiencies of extract equipment
- Contributes to a safe and pleasant working environment increasing employee morale
- Reduces contaminated air
This service is conducted in accordance with recommendations set out in the following regulations and guidance:
- Regulation EC852/2004 Enforcement of Regulation on the Hygiene of Foodstuffs
- Regulatory Reform (Fire Safety) Order 2005
- L24 Workplace Health, Safety and Welfare Regulation 1992 (revised 2013)
- RC44 Recommendations – Fire risk assessment of catering extract ventilation
- Loss Prevention Standard 2084 – Issue 1 – Standard for Inspection, Cleaning & Maintenance of
- Ductwork Systems
- NAAD21 – Part 1 Grease (Kitchen Extract)
- BESA TR19 Grease – Fire Risk Management of Grease Accumulation within Kitchen Extraction Systems
- BESA DW172: Specification for kitchen ventilation systems
The intention is to provide complete management and traceability of the kitchen extract systems in the premises, observations supported by photographs and wet film thickness test measurements taken to provide a comprehensive account of each extract installation.
Definition
The BESA TR/19 guidance defines kitchen extract ventilation systems as “the extract systems intended to collect and remove contaminants, heat and moisture produced by cooking equipment”.
Purpose
Commercial kitchen extract systems present particular hazards. As well as removing cooking odours and steam from the kitchen areas, the extract system removes greasy vapours from cooking appliances which are an ignition source.
Accumulated grease in an extract system forms a hidden combustion load – BESA TR19 Grease
During the cooking process, flammable vapour is given off from cooking oils at temperatures between 200 & 300 degrees centigrade. Spontaneous ignition occurs at 310-360 degrees centigrade – RC44 Recommendations for fire risk assessment of catering extract ventilation BSRIA.
Insurance companies will normally recommend a minimum frequency of extract ductwork cleaning, together with any terms and conditions to comply with the building’s insurance requirement.
This should include an assessment of business resilience. The Client has a “Duty of Care” to their clients, their employees and members of the general public under Health & Safety Regulation requirements.
The clean will include
Cleaning and degreasing of extraction canopy and filters, lights, plenum & ductwork, extraction fan and housing, exhaust unit and mesh.
Access panel installation may be required to service sections of ductwork otherwise inaccessible. (Details of which will be highlighted in the pre-clean service report).
The price includes the cost of all labour, materials, equipment, chemicals and the hire of specialist machinery necessary to complete the above work adhering to health & safety regulations.
Hot water and electricity are essential. The kitchen area should be cleared prior to an Insuraclean team visit as outlined in the quotation and booking confirmation.
The cost of cleaning will reduce with the implementation of a regular cleaning schedule.
The Report
Pre and Post images are taken to form part of the report which will follow the clean to clearly show the improvement and work carried out. This report will form part of the clients due diligence paperwork and will be supported by a certificate that can be shown to Fire Inspectors and Insurers that compliance requirements for the extract system have been fulfilled.
For more information please fill out our Contact Form or call 0333 207 2440